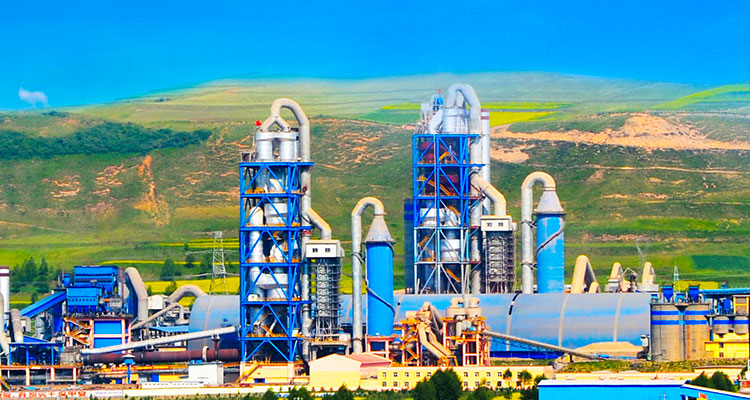
企業(yè)動態(tài)
平?jīng)龉举|(zhì)量管理改進創(chuàng)新成效顯著
發(fā)布日期:2014-04-30作者:jtdqgzb點擊量:2264次
本網(wǎng)訊 今年年初,平?jīng)龉境闪⑹炝蠌姸荣|(zhì)量控制攻關小組,有效解決了出窯熟料強度持續(xù)偏低、水泥混合材的摻加量受制約及水泥制造成本居高不下的問題。
技術攻關小組通過對進廠原燃材料、生料配料、水泥窯熟料煅燒等方面的系統(tǒng)分析和查閱相關資料,分析認為高硫煤、高氧化鎂及配料方案是影響熟料強度的主要原因,并采取三項具體的措施有效予以解決。一是與物流供應處溝通協(xié)調(diào)采用多礦點原煤搭配進廠,并對進廠原煤分礦點每旬檢驗全硫含量,控制原煤中全硫含量;二是加強礦山石灰石采礦層的質(zhì)量控制,針對不同采面石灰石品位進行搭配開采,并穩(wěn)定搭配剝離土,降低氧化鎂含量;三是大膽調(diào)整配料方案,采用高硅低鐵配料,并依照物料最佳液相量為24%的要求,逐步調(diào)整氧化鐵的指標,鐵質(zhì)原料消耗明顯下降,大大降低了生料制備成本。
經(jīng)過一段時間的檢測,熟料強度由2013年平均53.8MPa上升至2014年一季度的56.9MPa,而且水泥窯預熱器結皮量明顯減少,系統(tǒng)通風得到明顯改善,煅燒質(zhì)量進一步提高。
熟料強度的上升,不僅使水泥混合材摻加量上升,更有利于高品種水泥的生產(chǎn),今年在生產(chǎn)P.II52.5水泥時,對控制指標進行了調(diào)整:比表面積由400m2/kg降至360m2/kg,三氧化硫指標:由2.30%提高至2.70%,在粉磨過程中停加水泥助磨劑,水泥成本明顯下降,而且使P.II52.5水泥標準稠度下降,由2013年的29.5%下降至2014年一季度的27.8%。(汪芳玲)
技術攻關小組通過對進廠原燃材料、生料配料、水泥窯熟料煅燒等方面的系統(tǒng)分析和查閱相關資料,分析認為高硫煤、高氧化鎂及配料方案是影響熟料強度的主要原因,并采取三項具體的措施有效予以解決。一是與物流供應處溝通協(xié)調(diào)采用多礦點原煤搭配進廠,并對進廠原煤分礦點每旬檢驗全硫含量,控制原煤中全硫含量;二是加強礦山石灰石采礦層的質(zhì)量控制,針對不同采面石灰石品位進行搭配開采,并穩(wěn)定搭配剝離土,降低氧化鎂含量;三是大膽調(diào)整配料方案,采用高硅低鐵配料,并依照物料最佳液相量為24%的要求,逐步調(diào)整氧化鐵的指標,鐵質(zhì)原料消耗明顯下降,大大降低了生料制備成本。
經(jīng)過一段時間的檢測,熟料強度由2013年平均53.8MPa上升至2014年一季度的56.9MPa,而且水泥窯預熱器結皮量明顯減少,系統(tǒng)通風得到明顯改善,煅燒質(zhì)量進一步提高。
熟料強度的上升,不僅使水泥混合材摻加量上升,更有利于高品種水泥的生產(chǎn),今年在生產(chǎn)P.II52.5水泥時,對控制指標進行了調(diào)整:比表面積由400m2/kg降至360m2/kg,三氧化硫指標:由2.30%提高至2.70%,在粉磨過程中停加水泥助磨劑,水泥成本明顯下降,而且使P.II52.5水泥標準稠度下降,由2013年的29.5%下降至2014年一季度的27.8%。(汪芳玲)